Comprehending the Essentials and Applications of Plastic Extrusion in Modern Production
In the realm of modern-day production, the method of plastic extrusion plays a critical role - plastic extrusion. This complex process, involving the melting and shaping of plastic through specialized passes away, is leveraged throughout various industries for the production of diverse items. From car parts to durable goods product packaging, the applications are vast, and the potential for sustainability is equally outstanding. Untangling the principles of this procedure reveals the real adaptability and capacity of plastic extrusion.
The Fundamentals of Plastic Extrusion Process
While it may appear complex, the principles of the plastic extrusion process are based on fairly straightforward principles. It is a production process where plastic is melted and after that shaped right into a continuous profile through a die. The plastic extrusion process is thoroughly utilized in numerous markets due to its versatility, cost-effectiveness, and efficiency.
Different Sorts Of Plastic Extrusion Strategies
Building upon the basic understanding of the plastic extrusion process, it is necessary to explore the numerous methods associated with this production approach. The two key techniques are profile extrusion and sheet extrusion. In account extrusion, plastic is melted and created right into a continuous profile, commonly used to develop pipes, rods, rails, and window structures. On the other hand, sheet extrusion creates huge, flat sheets of plastic, which are generally more refined into products such as food product packaging, shower drapes, and car parts. Each strategy calls for specialized machinery and specific control over temperature level and pressure to make sure the plastic preserves its form throughout air conditioning. Understanding these methods is key to using plastic extrusion successfully in modern manufacturing.
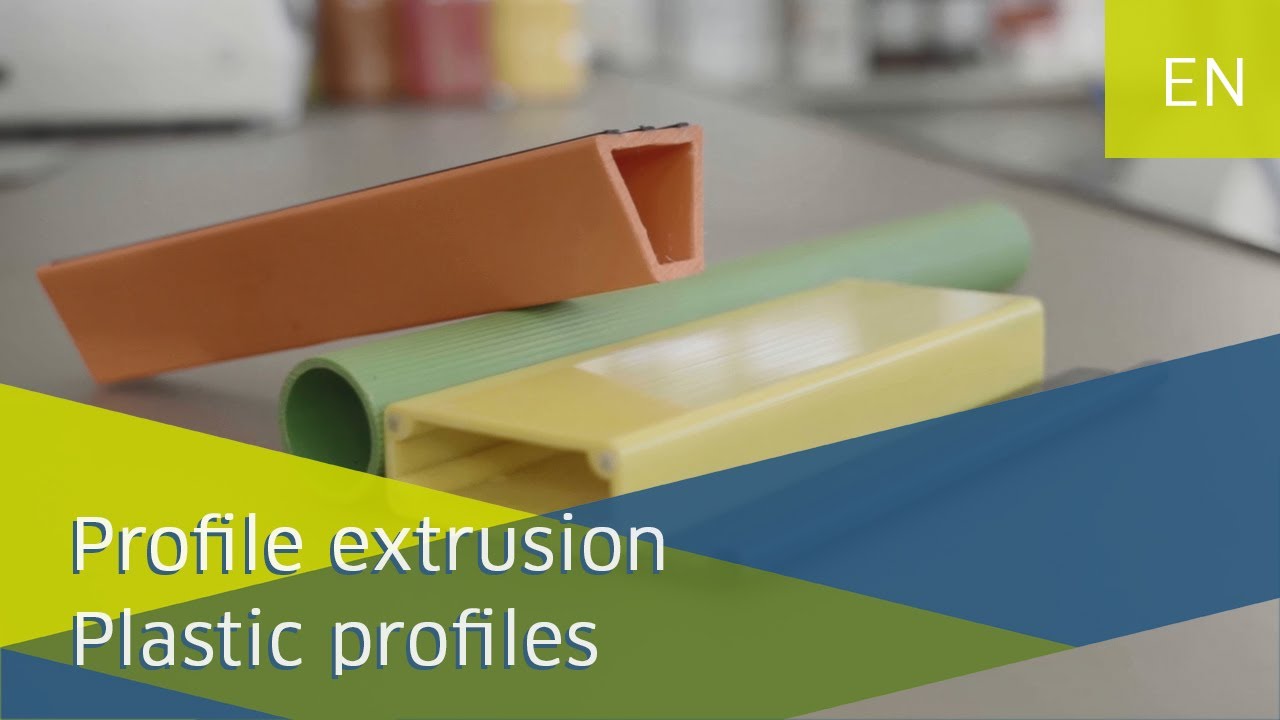
The Role of Plastic Extrusion in the Automotive Market
A frustrating majority of components in contemporary lorries are products of the plastic extrusion procedure. This process has actually transformed the vehicle industry, changing it into a more reliable, economical, and adaptable manufacturing field. Plastic extrusion is mainly used in the manufacturing of various automobile parts such as bumpers, grills, door panels, and dashboard trim. The procedure gives an uniform, regular outcome, enabling helpful hints manufacturers to generate high-volume get rid of excellent precision and marginal waste. The lightness of the extruded plastic components contributes to the total decrease in car weight, boosting gas performance. The sturdiness and resistance of these parts to warm, cool, and influence boost the durability of vehicles. Therefore, plastic extrusion plays a critical duty in automobile production.
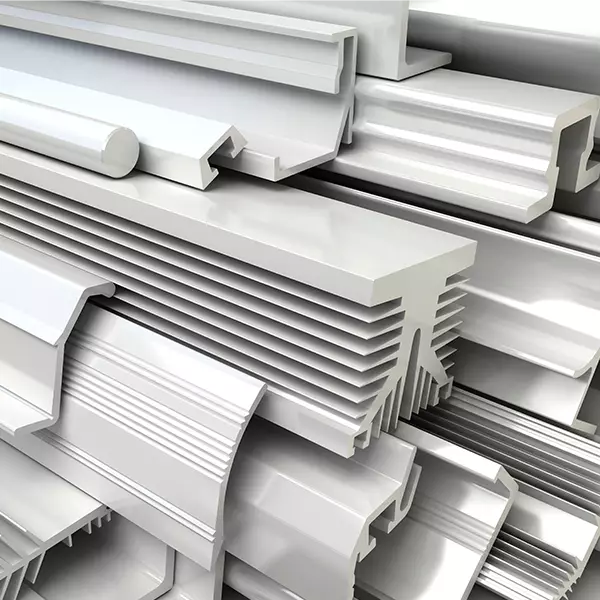
Applications of Plastic Extrusion in Durable Goods Manufacturing
Past its significant effect on the automobile industry, plastic extrusion shows equally effective in the realm of consumer products manufacturing. This process is vital in creating a wide range of items, from food packaging to family devices, toys, and also clinical gadgets. The versatility of plastic extrusion permits suppliers to make and produce intricate shapes and dimensions with high precision and performance. Moreover, as a result of the recyclability of numerous plastics, extruded elements can be reprocessed, lowering waste and cost. The versatility, flexibility, and cost-effectiveness of plastic extrusion make it see post a recommended option for many durable goods producers, adding considerably to the industry's development and innovation. However, the ecological effects of this extensive usage call for mindful consideration, a subject to be talked about additionally in the subsequent section.
Environmental Influence and Sustainability in Plastic Extrusion
The pervasive use of plastic extrusion in producing invites scrutiny of its ecological effects. Reliable machinery decreases power usage, while waste monitoring systems recycle scrap plastic, decreasing raw product needs. Regardless of these enhancements, even more development is required to mitigate the ecological impact of plastic extrusion.
Conclusion
In conclusion, plastic extrusion plays an essential function in contemporary production, particularly in the vehicle and durable goods markets. Its versatility permits the manufacturing of a variety of components with high accuracy. Moreover, its capacity for recycling and growth of biodegradable materials supplies an appealing method in the direction of sustainable practices, thus resolving ecological concerns. Comprehending the essentials of this procedure is key to optimizing its applications and advantages.

The plastic extrusion process is thoroughly utilized in numerous markets due to its cost-effectiveness, performance, and flexibility.
Structure upon the fundamental understanding of the plastic extrusion process, it is needed to discover the different techniques included in this manufacturing method. plastic extrusion. In comparison, sheet extrusion produces big, level sheets of plastic, which are usually additional processed into items such as food packaging, shower drapes, and car components.An overwhelming bulk of parts in modern lorries are products of the plastic extrusion procedure